Unveiling the Secrets: How Flush Mount LED Lights Are Made in China and What Truly Matters for Quality and Design
Flush mount LED lights have become a cornerstone of modern lighting solutions, known for their sleek design and energy efficiency. These fixtures are not just stylish; they play a crucial role in enhancing the ambiance of homes, offices, and commercial spaces. With the rapid shift towards energy-saving technologies, the demand for flush mount LED lights has skyrocketed. A significant portion of these lights is manufactured in China, which has established itself as a global hub for LED production. In this article, we will delve into the intricate manufacturing process of flush mount LED lights in China, examining the various stages involved and the critical factors that influence their quality and design.
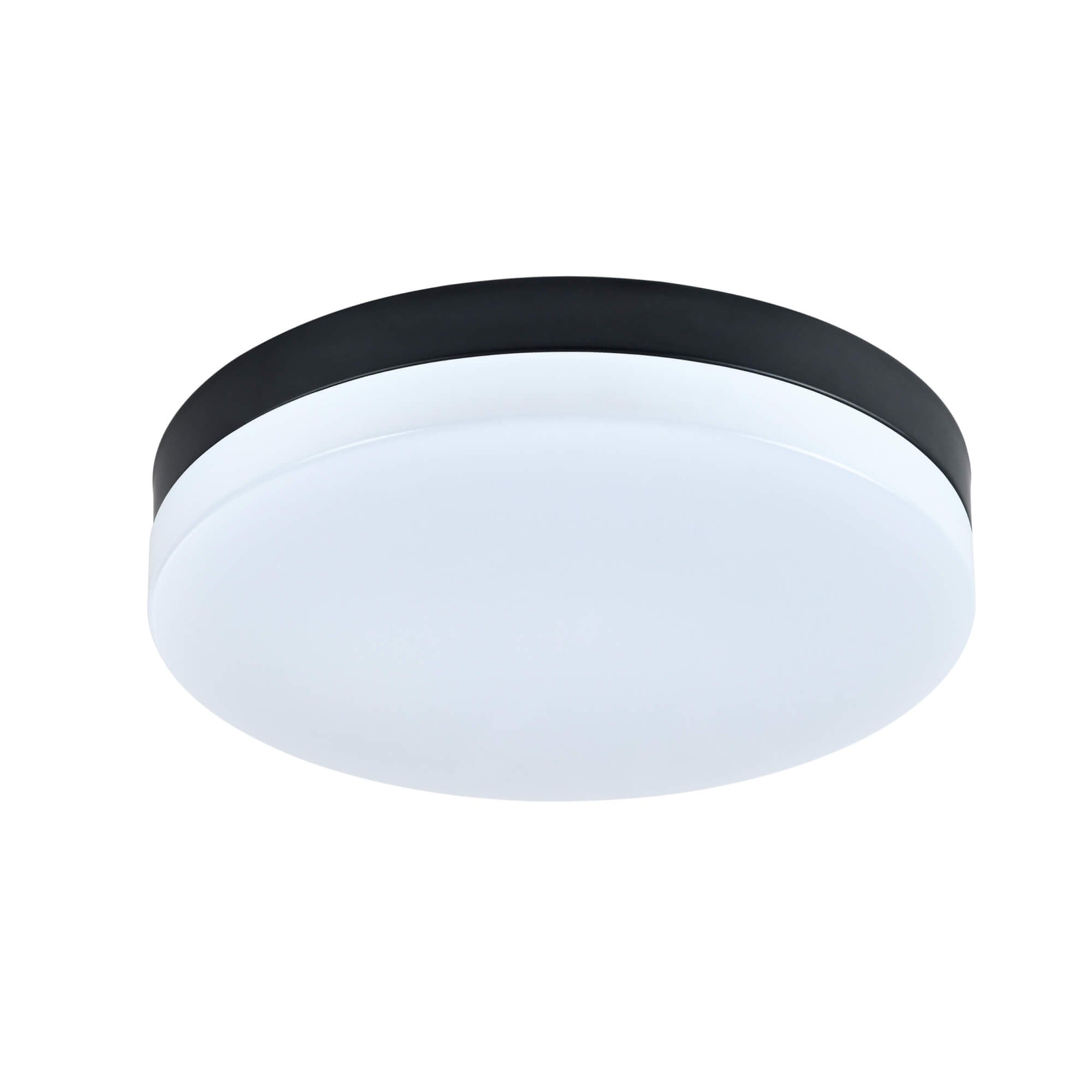
The Manufacturing Process of Flush Mount LED Lights in China
The manufacturing process of flush mount LED lights in China is a meticulously orchestrated blend of design, engineering, and craftsmanship. It begins with the design phase, where innovative ideas are transformed into tangible products. This is followed by sourcing high-quality materials, assembling the components, and implementing rigorous quality control measures. Each of these steps is vital to ensuring that the final product meets the high standards expected by consumers around the world.
Design and Prototyping
The journey of a flush mount LED light begins with the design and prototyping phase. Designers and engineers collaborate to create products that are not only visually appealing but also functional and energy-efficient. They consider various factors such as size, shape, and color temperature to ensure that the lights fit seamlessly into diverse environments. Prototyping allows for testing different designs and configurations, ultimately leading to a final product that balances aesthetics and performance. I once visited a friend's design studio, where I witnessed the brainstorming sessions where ideas evolved into prototypes, showcasing the creativity that drives this industry.
Material Sourcing
Once the design is finalized, the next step is material sourcing. This phase is crucial as the quality of materials significantly impacts the durability and performance of the flush mount LED lights. Manufacturers typically use components such as aluminum for heat dissipation, polycarbonate for lenses, and high-quality LED chips for optimal brightness and energy efficiency. Establishing reliable supply chains for these materials can make a substantial difference in product quality. A friend who works in the procurement field once shared how careful selection of suppliers has helped their company avoid costly quality issues, highlighting the importance of this step in the manufacturing process.
Assembly Process
The assembly process of flush mount LED lights is where all the hard work comes together. This stage often employs both advanced technology and skilled labor to ensure precision. Automated machines may handle tasks such as soldering and testing, while skilled workers assemble the final product by integrating various components. The balance of technology and human expertise is essential to meet production demands while maintaining quality. I remember visiting a factory where I saw firsthand how workers meticulously assembled lights, showcasing their dedication to craftsmanship.
Quality Control Measures
Quality control is a critical component of the manufacturing process. After assembly, flush mount LED lights undergo rigorous testing to ensure they meet safety and performance standards. Quality control measures can include visual inspections, electrical testing, and longevity tests to simulate years of use. Implementing these measures not only assures manufacturers of product reliability but also builds consumer trust. A family member who once worked in quality assurance shared stories of how thorough testing processes saved their company from potential recalls, underscoring the importance of maintaining high-quality standards in production.
Insights on Manufacturing Quality and Design
In conclusion, understanding the manufacturing process of flush mount LED lights in China provides valuable insights into what influences product quality and design. From the initial design phase to rigorous quality control measures, each step is integral to creating high-quality lighting solutions that meet consumer expectations. As the demand for energy-efficient and aesthetically pleasing lighting continues to grow, recognizing the factors that contribute to the production of these lights becomes increasingly significant for consumers and stakeholders alike. By appreciating the craftsmanship and diligence involved in the manufacturing process, we can make informed choices about the lighting solutions we bring into our spaces.